24/01/11
Voltage Options in Off-Highway Machinery
Voltage Options in Off-Highway Machinery: Unraveling the Low Voltage vs. High Voltage Dilemma
In the fast-paced world of off-highway machinery, the decision between low-voltage and high-voltage systems is a make-or-break factor influencing performance, efficiency, and safety. To navigate this complex terrain successfully, it’s crucial to understand the differences between these two voltage options.
Decoding Low Voltage and High Voltage:
Low-voltage systems are capped at 30Vac or 60Vdc. For lighter off-highway applications, think battery levels of 120Vdc or lower – that’s the low-voltage realm. On the flip side, high-voltage systems, especially prevalent in mining and construction, kick in above 120 volts, sometimes reaching a whopping 1000Vdc or more. So, before settling on a battery voltage, consider the power needs and application requirements.
Advantages of Low Voltage:
Low-voltage systems come with their perks, making them a staple in the off-highway world:
- Safety First: Lower voltage means lower risks of shocks, arcs, and fires – creating a safer environment for operators and tech wizards.
- Budget-Friendly: Machines designed for low voltages are usually lighter on the wallet, both initially and in the long run.
- Reliability Standard: A trusted solution with a proven track record, easily understood by techies and machine operators.
- Keeping It Simple: Simple design equals easy troubleshooting, repairs, and maintenance – less downtime and fewer expenses.
- Fun Fact: Did you know? Recent advancements include IPM motor technology for high efficiency in a compact design.
Low-voltage systems commonly power scenarios with a 20 kW cap. Picture electric tractors, utility terrain vehicles, automated guided vehicles – these are the low-voltage champions. But, be wary, their strengths might falter when tackling high-performance, energy-hungry machinery.
Advantages of High Voltage:
High-voltage systems are stealing the spotlight in the off-highway arena, and here’s why:
- Power Surge: Perfect for heavy-duty machinery, offering more power and efficiency for top-notch productivity.
- Tech Talk: Allows fancy tech integrations like electric propulsion and regenerative braking, cutting down on fuel consumption and emissions.
- Future-Proof: Ready to tackle future regulations and environmental standards, setting companies up for the long haul.
- Efficiency Boost: Less heat loss during energy conversion means an efficiency boost overall.
For the heavy-duty players and fully electric chassis, high voltage is the go-to. Smaller tools that crave less power can either sip directly from the primary high-voltage source or indulge in a DC/DC converter. The choice? It depends on factors like cost, availability, and how complicated you want the integration dance to be.
In a Nutshell:
Choosing between low voltage and high voltage boils down to your specific needs, machine requirements, and safety concerns. While low voltage rocks the reliability boat, high voltage takes the lead in power and keeping up with industry trends.
Adigo Drives Solutions:
Whether you’re diving into low or high voltage, count on us to cater to your electrical whims. Our commitment to delivering comprehensive solutions has led us to embrace both low and high voltage in our product range. Plus, we tests both LV and HV components, ensuring top-tier quality and supporting partners in crafting complete solutions for their gear. Trust Adigo Drives for innovative solutions driving excellence in the fiercely competitive off-highway landscape.
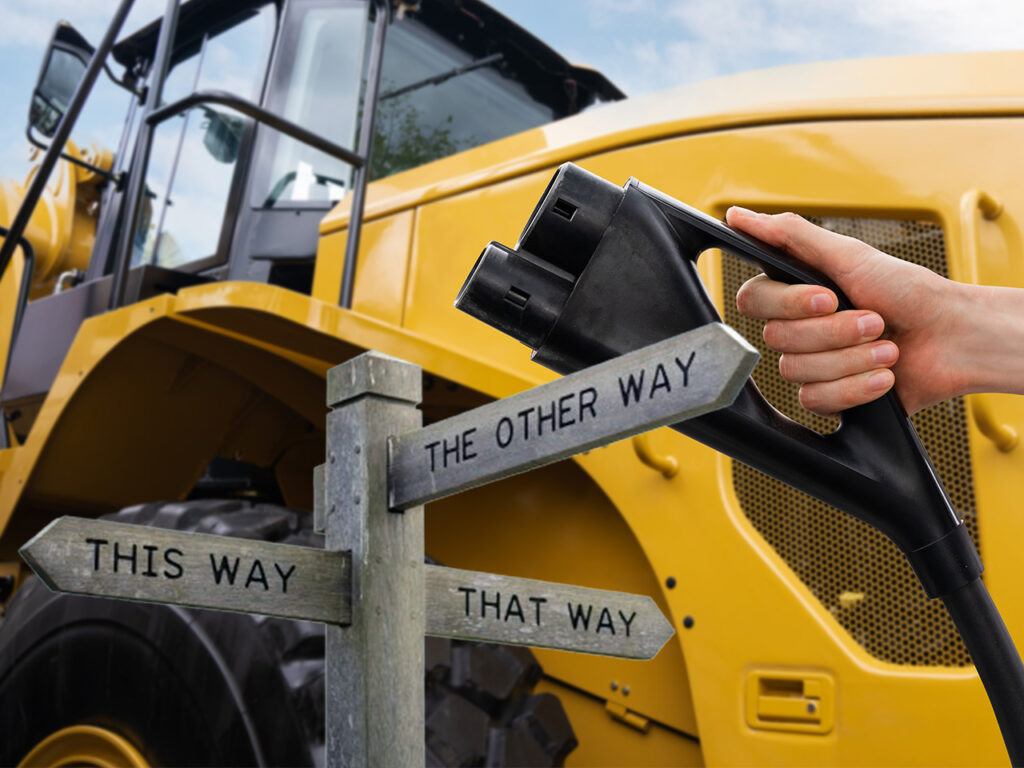
Read more>