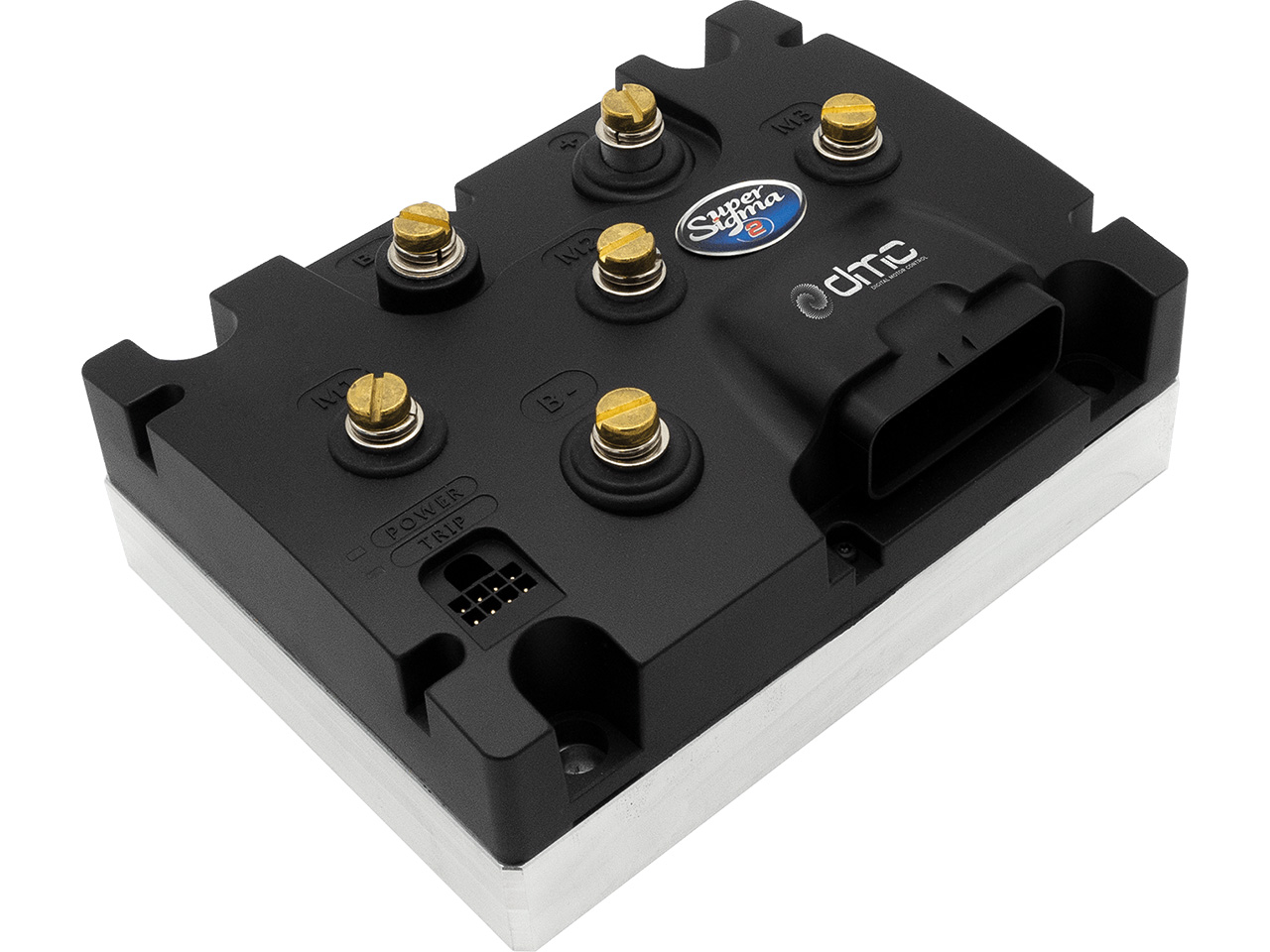
24/01/30
Elevate Electric Vehicles with DMC’s Motor Controllers
Elevate Your Electric Vehicles with DMC’s Versatile Motor Controllers!
In the dynamic world of electric vehicles, DMC (Digital Motor Control) GmbH shines as a beacon of innovation, offering advanced motor controllers that breathe life into your battery-powered dreams. With over two decades of expertise under our belt, DMC meticulously engineers controllers that seamlessly integrate with a diverse array of electric vehicle applications, from Material handling and Off highway machines to golf carts, forklifts, marina applications and beyond.
DMC’s Motor Controllers: Your Gateway to Unmatched Performance
Step into the future with DMC’s comprehensive motor controller portfolio, a unified platform designed to cater to a wide spectrum of applications. Our controllers effortlessly manage various three-phase motor technologies, including permanent magnet synchronous motors (PMSM), interior permanent magnet motors (IPM), reluctance motors (PMAC), and switched reluctance motors (SRM) to name a few.
Power Your Electric Vehicles with Precision
Whether it’s traction or pump control, DMC’s motor controllers excel in both domains. With versatile capabilities that allow you to seamlessly switch between speed and torque modes, you can tailor your controller’s performance to meet the exact requirements of your electric vehicle. Also make use of our Sensor less motor possibilities.
Unleash the Power of Reliability and Flexibility
DMC understand the demands of real-world applications. That’s why our motor controllers are built to last, boasting robust construction and reliable components that can weather any storm. Our flexible software architecture enables easy customization and optimization, ensuring your vehicle operates at peak performance.
Simplify Optimization with the DMC Configurator
Say goodbye to complexity with our revolutionary DMC Configurator software. This intuitive tool streamlines the motor tuning, sensor autotuning and communication setup so you can configure your controller with precision and ease.
Seamlessly Integrate with VCU and BMS
DMC’s motor controllers aren’t just about power delivery; they can act as intelligent vehicle control units (VCUs) in their own right. With integrated logic, you can independently control smaller vehicles, while seamless integration with the battery management system (BMS) ensures safe operation of lithium batteries. Today we support from start BMS integration from: Micropower LionBrix, Vanguard, Cellpower, Flash Battery, Lionic, to name some.
Connect with Industry-Standard Protocols
Ensure seamless vehicle integration with DMC’s motor controllers, which communicate effortlessly with your vehicle’s VCU/ECU using industry-standard protocols like CANopen or J1939. Experience a smooth, integrated driving experience like never before.
Partner with Adigo and DMC for Excellence in Electric Mobility
Join forces with Adigo and embark on a journey of innovation. Let us elevate your electric vehicles to new heights of performance, efficiency, and versatility. Together, we can shape the future of electric mobility.
Explore our offering here:
DMC Supersigma2 motor controller
DMC SigmaLITE motor controller
Ready to Drive Change?
Discover the power of electrification with Adigo today. Click below to learn more and take the first step towards a brighter, greener future!
Learn More About Motor Control here.
Read more>