23/06/29
The Power of Electrification: Motor Type Comparison
As the world embraces electrification solutions, the choice of electric motor becomes crucial in driving efficient and sustainable machinery. The market is flooded with various motor types, each with its own unique set of advantages. We will delve into the realm of motor types and provide a quick way to compare all of them.
Optimizing Motor Selection
Selecting the ideal motor for your electric machinery can prove challenging. It’s crucial to remember that a motor should not be chosen arbitrarily; instead, you must thoughtfully evaluate various options and find the one that best suits your system. Unfortunately, many individuals overlook the significance of an electric system, opting for a standard motor, which undermines the essence of having an electric machine.
Synchronous IPM:
Utilize permanent magnets, specifically neodymium-iron-boron magnets, in their rotors. These magnets enhance power density and allow for the utilization of reluctance torque, reducing the required magnet material. However, this design leads to high costs despite the high-power density achieved.
Synchronous SPM:
Incorporate a rotor composed of low-loss magnetic laminated sheets and rare earth surface magnets. These internal features enable high power density and precise operation, supported by reliable position sensors. While these motors offer constant torque, their speed is limited, presenting a drawback in terms of high-speed applications.
Synchronous Reluctance:
Operate without permanent magnets, making them cost-effective but requiring higher current. There are two types: switched reluctance motors and synchronous reluctance motors. The former offer improved torque ripple and efficiency compared to the latter. While synchronous reluctance motors deliver nice performances, they can be challenging to drive.
Synchronous Separately Excited:
Differ from traditional motors with permanent magnets. They utilize copper windings instead, enabling control over the rotor’s magnetic field by adjusting the current in the windings. While these motors offer competitive cost advantages, they can be challenging to drive efficiently.
Asynchronous Induction:
Operates with a rotating field that lags behind the rotor, causing asynchronous rotation. This time difference induces voltage in the short circuit cage, resulting in a magnetic force on the rotor. While these motors are cost-effective, they suffer from lower efficiency compared to other types.
Axial Flux:
Come in two variants: dual-rotor single stator and single-rotor dual-stator. These machines offer higher torque per motor volume compared to radial motors because the magnetic surface area is concentrated on the rotor face rather than the outer diameter. However, achieving this high-power density comes at a considerable cost.
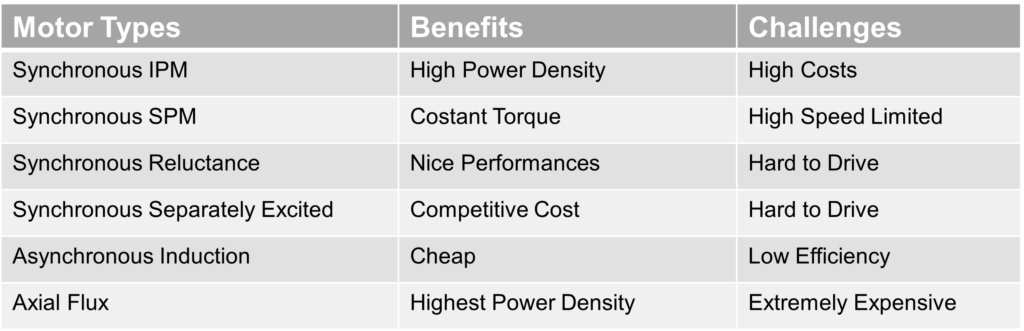
The Benefits of Switching to IPM Motors
New technologies as IPM motors have been launched to help reduce fuel consumption and pollution. In comparison to AC motors, IMP motors are a greener choice for a more sustainable future.
Read more about the benefits of IPM motors:
Compact: IPM Motors have a smaller size and fewer coils, resulting in higher power density and a smaller motor overall. Additionally, they have improved heat transfer and simplified cooling systems.
Modular: IPM Motors are Permanent Magnet Synchronous Motors that do not require brushes or consumable parts, resulting in lower maintenance costs.
Lightweight: IPM Motors weigh only one-third of conventional motors. For example, a 10kW IPM motor typically weighs less than 22kg.
High Torque: IPM Motors have higher full-load efficiency compared to AC induction motors. The rotor is made of permanent magnets, resulting in high efficiency and reduced heat generation due to the absence of coils.
Efficient: IPM Motors can be installed in narrow spaces, offering a more compact mechanical package. This makes them highly suitable for applications where space is limited.
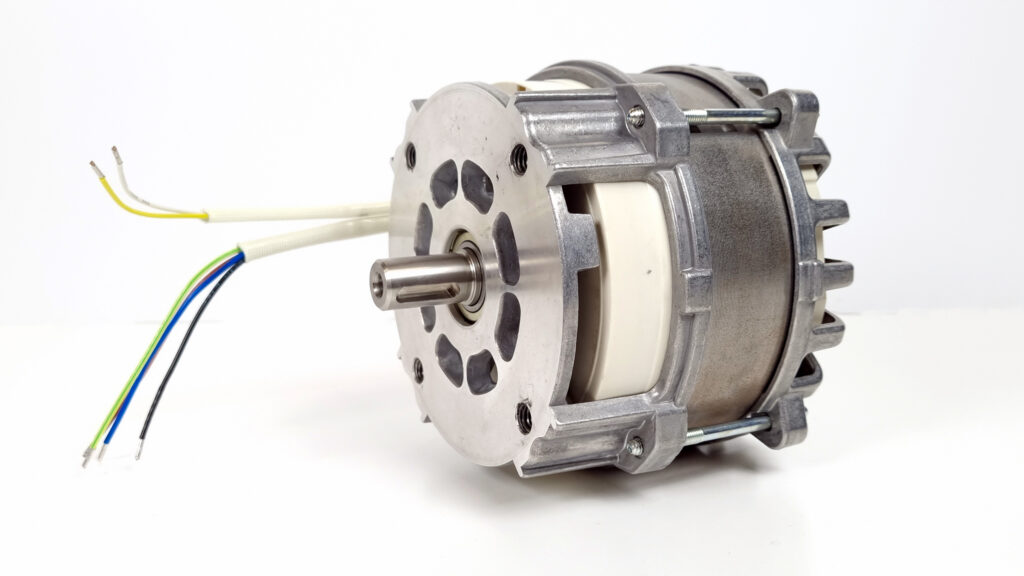
Read more>