24/03/13
Unlocking the Potential of Lithium Battery Systems
Unlocking the Potential of Lithium Battery Systems for Battery-Powered Vehicles
At Adigo Drives, we pride ourselves on being at the forefront of electrification solutions. Serving as a hub for innovation and technology, we cater to the needs of companies across Northern Europe, offering comprehensive lithium battery systems for a wide range of applications, including construction machinery, material handling, airport equipment, municipal machines, mining machines, and more. Our approach is rooted in the belief that we are the leading provider in our field, offering unparalleled expertise and solutions to companies seeking to electrify their operations.
Understanding Lithium Battery Technology
Lithium-ion batteries have emerged as the preferred choice for powering battery-operated vehicles due to their high energy density, lightweight design, and long cycle life. These characteristics make lithium-ion batteries ideal for applications where efficiency, reliability, and performance are paramount. At Adigo, we offer standard battery packs from Vanguard and build custom-made battery packs with Micropower modules, tailoring our solutions to meet the unique needs of each client and application.
Safety Standards and Compliance
Ensuring the safety of lithium battery systems is of utmost importance to us. We adhere strictly to industry standards and regulations, such as those set by the IEC, UN, ISO, governing the design, manufacturing, and deployment of battery-powered vehicles. Our team of experts stays abreast of the latest developments in safety protocols and incorporates them into our battery systems to mitigate risks and ensure safe operation in diverse environments.
Integration of CAN Communication
One of the key features of our lithium battery systems is the integration of Controller Area Network (CAN) communication technology. CAN communication allows seamless communication between various components of the vehicle, including chargers, motor controllers, Vehicle Control Units (VCUs), Electronic Control Units (ECUs), and other onboard computers. This integration enhances system efficiency, performance monitoring, and diagnostic capabilities, through IoT devices, leading to optimized operation and maintenance of battery-powered vehicles. Furthermore, CAN communication contributes to safety by enabling precise control over battery charging and energy regeneration for the electric motor.
Optimizing Performance and Efficiency
Our lithium battery systems are engineered to deliver exceptional performance and efficiency across a wide range of applications. Through advanced battery management systems and intelligent charging algorithms, we maximize the usable capacity of the battery while prolonging its lifespan. This optimization ensures that battery-powered vehicles operate at peak performance levels, resulting in increased productivity and reduced downtime.
Maintenance Best Practices
Proper maintenance is essential for ensuring the longevity and reliability of lithium battery systems. Here are some best practices to follow:
- Regular Inspections: Conduct routine inspections to check for signs of wear, damage, or abnormal behavior. Inspect battery connections, terminals, and wiring for any anomalies and address them promptly.
- Temperature Management: Maintain optimal operating temperatures for the battery to prevent overheating or freezing, which can degrade performance and shorten lifespan. Implement thermal management systems to regulate temperature fluctuations and ensure consistent operation.
- Charge Management: Follow recommended charging practices to avoid overcharging or deep discharging, which can damage the battery and affect performance. Utilize smart charging solutions that monitor battery status and adjust charging parameters accordingly.
- Storage Conditions: Store batteries in a cool, dry environment away from direct sunlight and moisture. Proper storage conditions help preserve battery health during periods of inactivity and prevent degradation due to environmental factors.
Our Trusted Battery Suppliers
At Adigo Drives, we partner with leading battery manufacturers to ensure the highest quality and reliability of our battery systems. Two of our trusted suppliers include:
Micropower: Micropower Group specializes in the production of high-quality lithium-ion batteries modules that can be tailored to the specific needs of our customers. Their batteries are characterized by their advanced technology, compact design, and long service life, making them a preferred choice for our diverse range of applications. Read more here.
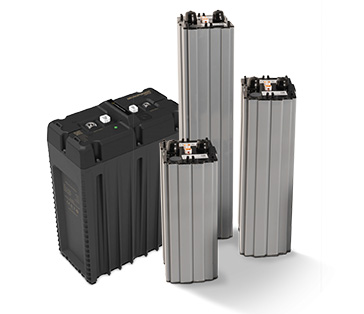
Vanguard: Vanguard Power Systems is a renowned manufacturer of lithium-ion battery systems, offering a wide range of products designed for various applications. Their batteries are known for their exceptional performance, durability, and safety features, making them an ideal choice for our simpler battery-powered vehicles and accessories in the industry. Read more here.
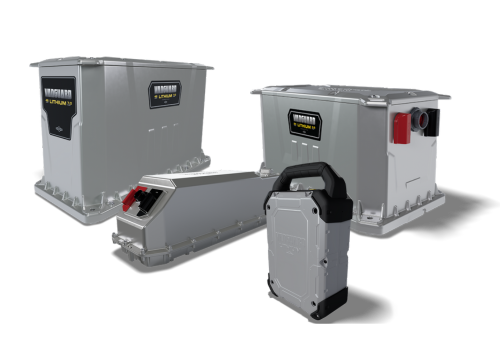
To conclude…
At Adigo Drives AB, we offer comprehensive solutions as system integrators, leveraging our expertise in lithium battery technology and industry-leading partnerships to deliver innovative electrification solutions to our customers. Whether you’re in the market for AGVs, material handling equipment, off-highway machinery, or ground support equipment, we have the expertise and resources to meet your needs effectively.
If you have any questions or would like to discuss your specific needs, please don’t hesitate to contact us at Adigo. We’re here to help!
Read more>